Hi 👋 - Happy Sunday. Redundancy is nature’s insurance policy. In business, it’s a dirty word. This post explores the clogged Suez Canal, just-in-time inventory and supply chain disruptions. Thanks for reading. ⛴
Many new readers discover Below the Line when a friend or coworker forwards it to them. If you enjoyed this post, please consider sharing it:
If you aren’t subscribed yet, you can subscribe here:
Forrest Gump said it best: shit happens. Always has, always will.
On March 23, the Ever Given, a container ship the size of the Empire State Building, ran aground in the Suez Canal. The initial take is that strong winds and poor visibility caused the snafu. While a boon for meme creators and amateur web developers, the incident is no laughing matter.Â
The Suez Canal connects the Mediterranean and Red Sea, shaving ten days off the trip between Asia and Europe. It’s a shortcut for manufactured goods from Asia and oil from the Middle East to Europe. A vital artery, about 10% of global trade sails through it each year1.Â
Dislodging the Ever Given could take a week or more. In the meantime, ships are piling up at both ends of the canal, billions of dollars of inventory sit idle and containers are in short supply. Minute by minute, the economic toll mounts.Â
Just-(Not)-In-Time
The beached Ever Given could bring factories to a standstill. That’s because modern manufacturing processes provide little buffer stock. Lean manufacturing and just-in-time inventory rely on receiving goods only when needed. Supplier networks become an extension of factories. This works when supply chains are operating smoothly. The tradeoff is heightened vulnerability to disruptions, which is only a strong gust of wind away.Â
Just-in-time was developed by Toyota in the 1960s and 1970s to reduce waste and improve efficiency. The Toyota Production System aims to make what is needed, when it is needed, and in the amount needed2. The system powered Toyota to become a leading automaker and has gone global.
A lesson from Toyota is that lower inventory levels improve profitability. Inventory costs money to purchase and warehouse. It can become obsolete, spoil, or go out of style. Additionally, there’s an opportunity cost: money tied up in inventory isn’t producing returns, like goods currently idling in the Suez Canal. Reducing inventory frees up capital, improves cash flow and boosts margins. So far, so good. Â
The downside of lower inventory levels are increased operational risk and susceptibility to disruption. Inventories act as a buffer, absorbing supply shocks. Just-in-time manufacturing requires producers to accurately forecast demand. Yet predictions are hard, especially when they’re about the future. While manmade and natural disasters are facts of life, they’re typically not incorporated into corporate planning. Few analysts accounted for the Suez Canal shutting down in their 2021 plans.Â
The Ever Given may prove to be a minor disruption, but examples of supply chain shocks abound. In 2011, the trifecta of an earthquake, a tsunami and damage at the Fukushima nuclear plant hindered Japanese semiconductor fabrication, impacting automobile and electronics production3. The same year, flooding in Thailand crippled the hard-drive market, impacting PCs and servers4. Shocks are impossible to predict, but guaranteed to occur.Â
Two Ears, Two Eyes, One Integrated Circuit
Supply disruptions aren’t going away. Complex, intertwined supply chains are ripe ground for lollapalooza effects. With little slack, small issues can cascade. One coping mechanism is adding redundancy. For example, using multiple suppliers in different geographies and carrying more inventory.Â
While redundancy has a negative connotation in businesses, nature loves it. Survival is a prerequisite for success and evolution aims to ensure survival. Evolution gave humans two ears, two eyes, two kidneys, two lungs and a bevy of other pairs. Mother Nature produces few cyclops5. As mathematician and former derivatives trader Nassim Nicholas Taleb points out in his excellent book Antifragile:Â Â
Nature likes to over-insure itself. Layers of redundancy are the central risk management property of natural systems.
Redundancy makes a system less prone to failure, at a cost. In systems design, redundancy increases weight, size and power consumption. It’s similar in biology. Lugging around two lungs burns more calories. In business, redundancy raises costs. Carrying more inventory makes a business more resilient, but it's also more expensive. Taleb is clear-eyed about this tradeoff:
Redundancy is ambiguous because it seems like a waste if nothing unusual happens. Except that something unusual happens - usually.
The Suez Canal is usually open, for instance. It’s easy to envision a spreadsheet jockey analyzing a blueprint of the human body and concluding: removing a lung and a kidney will cut operating expenses by 15.74% while not impairing performance under normal operating conditions. Great ROI, until shit happens and you need to sprint.
Redundancy is like insurance: an expense you pay but hope to never use. Carrying extra inventory is less efficient in the short-run, but can make a business more effective in the long-run. Great businesses like Berkshire Hathaway and LVMH use crises as opportunities to gain market share. Acting opportunistically requires a stock of dry powder.Â
Businesses would be wise to take more cues from nature. Incomprehensible and unexpected interactions are characteristics of complex systems like global supply chains. Natural disasters are a common cause of supply disruptions. As the climate warms, there’s a growing consensus that weather will become more extreme, portending more natural disasters. Investors and financial regulators are already pressing companies to disclose how climate change affects business6. When 100-year floods happen once a century, you get a mulligan. When they happen more frequently, you don’t.Â
The Ever Given is beached, but it will still leave a wide wake.Â
Newsletter Spotlight
Written by Jared Holst, Brands Mean a Lot is a once-a-week commentary on the ways branding impacts our lives. Each week, he explores contradictions within the way politics, products, and pop-culture are branded for us, offering insight on what’s really being said. Check out his recent post - the first in a series entitled The Bullshit Economy. In it, Jared explores how bad economics and poor policy, rather than market needs, has given rise to startups who offer home ownership to those who can’t afford it. Subscribe here.
More Good Reads
NYT Suez Canal 101. Reuters on the wide ranging impact of natural disasters in Japan on global supply chains. Below the Line on why catastrophes are an inherent part of complex systems.Â
For more like this once a week, consider subscribing 👇
👉 If you enjoyed reading this post, please share it with friends!
Disclosure: This post contains an Amazon affiliate link. If you’re interested in reading Antifragile, purchasing through this link supports Below the Line. The author owns shares in Berkshire Hathaway and thinks it’s a fantastic business.Â
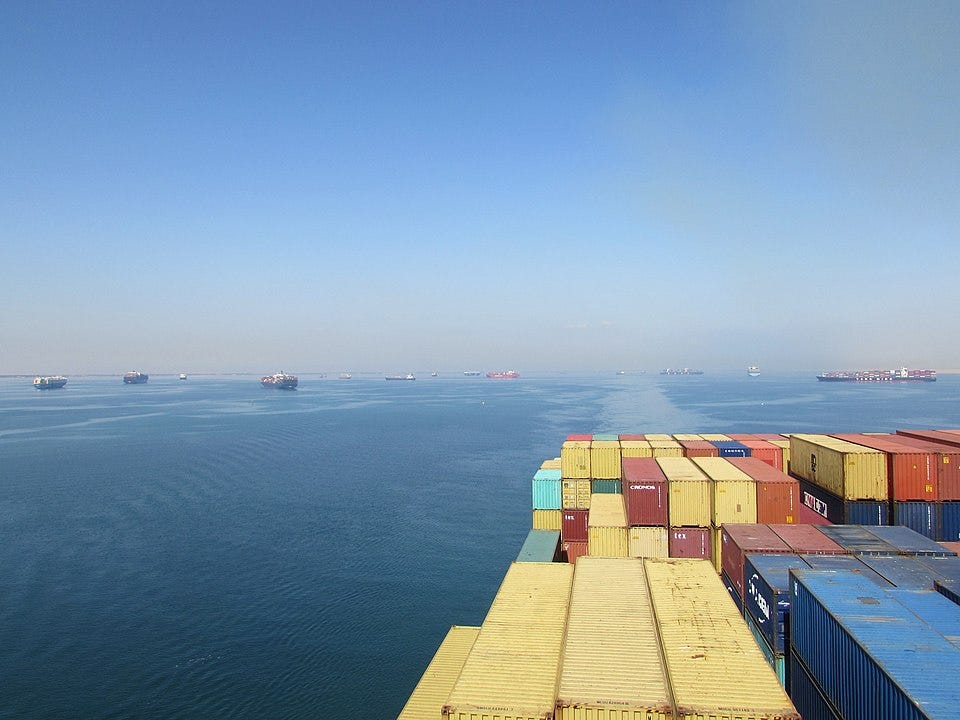
The New York Times, In Suez Canal, Stuck Ship Is a Warning About Excessive Globalization, March 26, 2021.Â
Toyota, Toyota Production System, March 27, 2021.Â
Reuters, Special Report: Disasters show flaws in just-in-time production, March 21, 2011.
The New York Times, Thailand Flooding Cripples Hard-Drive Suppliers, November 6, 2011.Â
Washington State University, Ask Dr. Universe: Are there creatures on Earth with one eye? -Elena, 7, Vancouver, Canada, 2018.
The Economist, Regulators want firms to own up to climate risks, March 13, 2021.
Lung for sale, link in bio